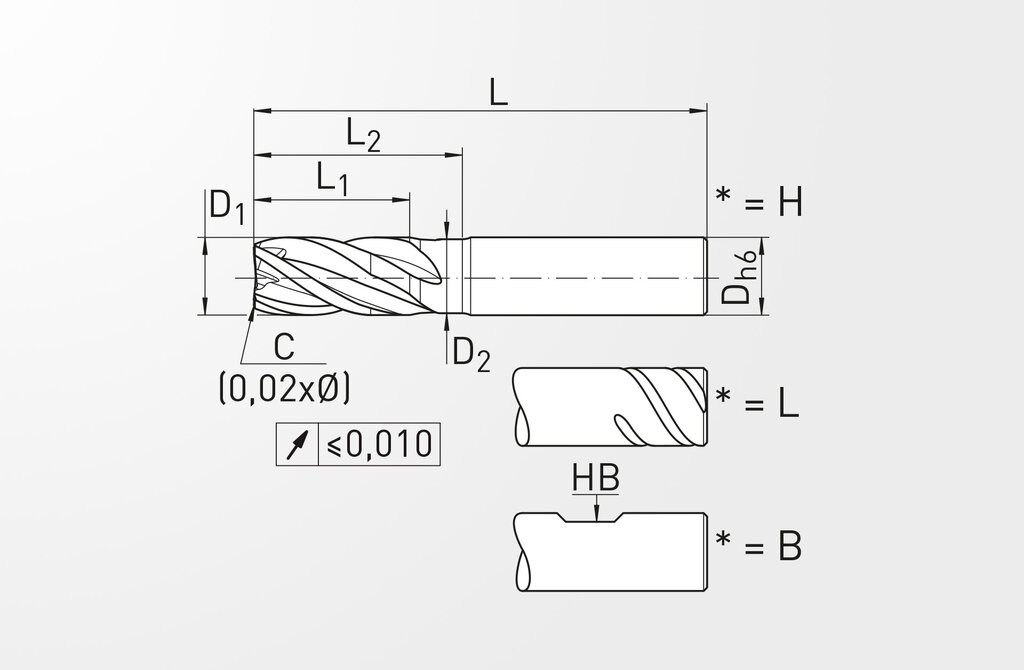
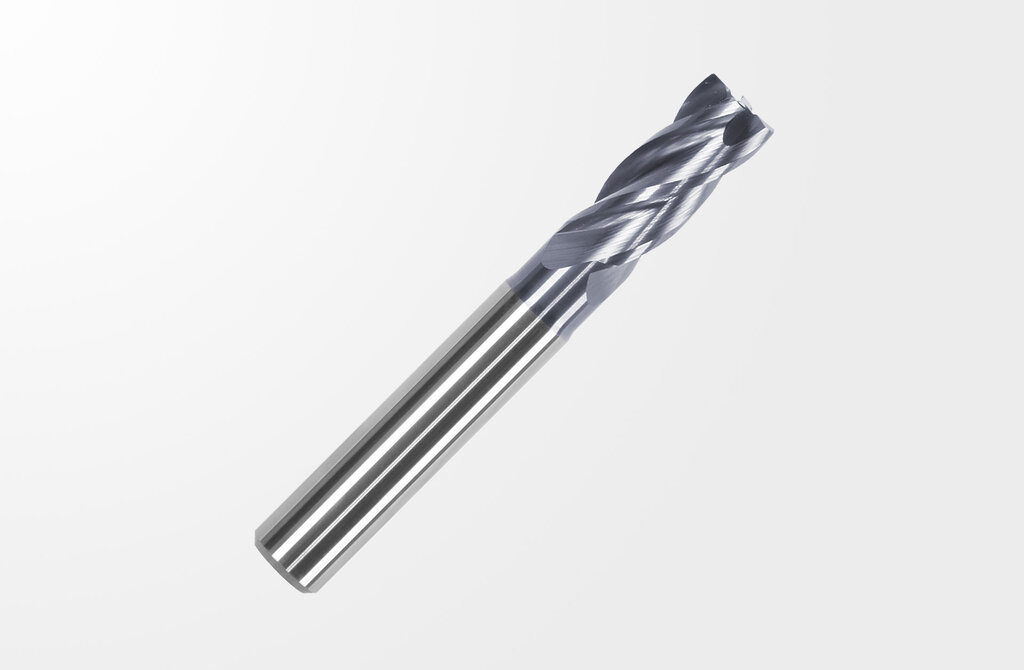
Characteristics
Applications
Areas of application-material
Description
HAIMER MILL - F2004NN Chamfer
Solid carbide end mill
Quality pass
Shank tolerance h6
Runout < 0.0004" (10 µm)
Universal solid carbide end mill for a broad range of applications
- Shank tolerance: h6
- Neck for higher cutting depth
- Center cutting
- Unequal cutting edge
- Unequal Helix
- Runout < 10 µm
- For almost all materials
- For roughing and finishing
- For ramping, drilling and slotting
HAIMER TIP
Cooling with Cool Jet or Cool Flash and using Power Chucks is recommended for higher tool life and high removal rate.
Technical specifications
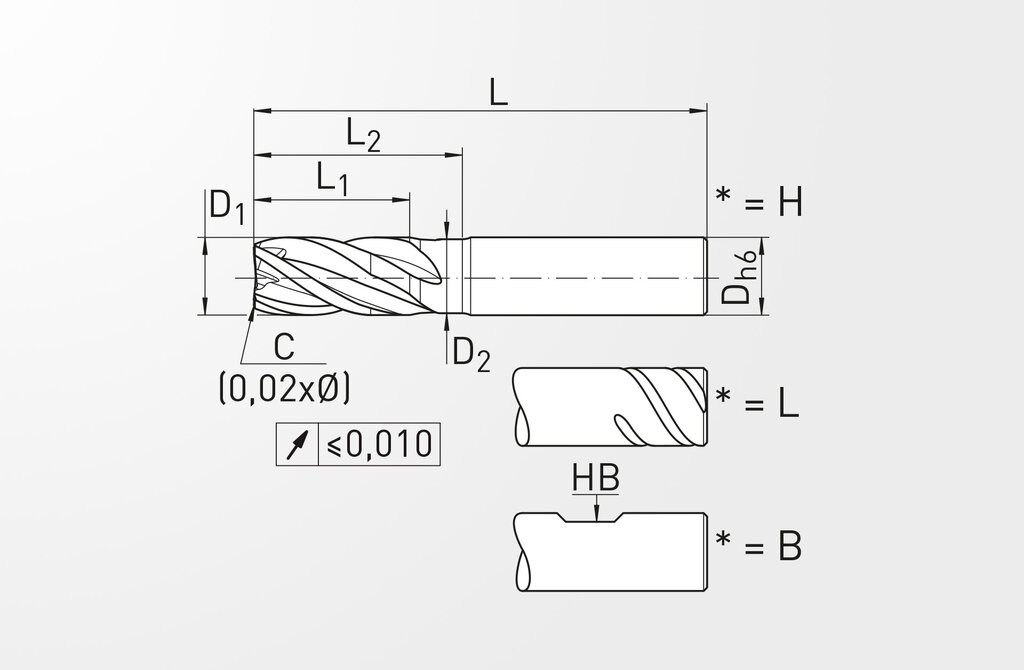
Notice
Technical data subject to change without prior notice.
Description | Norm: HAIMER | Value: metric/inch |
---|---|---|
Cutting edge diameter | D1 | 10 mm / 0.394 inch |
D1 Tolerance | f9 | |
Number of cutting edges | Z | 4 |
Corner design | C | |
Chamfer size | C | 0,2 mm / 0.008 inch |
Chamfer angle | W | 45 ° |
Length of cutting edge | L1 | 22 mm / 0.866 inch |
Overalllength | L | 73 mm / 2.874 inch |
Neck diameter | D2 | 9,5 mm / 3/8 inch |
Neck length | L2 | 30,5 mm / 1.201 inch |
Shank diameter | D | 10 mm / 0.394 inch |
Shank version | Glattschaft | |
Helix angle | 31/33 ° | |
HAIMER Material | D | |
HAIMER Coating | A |
Description | Norm: DIN 4000 | Value: metric/inch |
---|---|---|
Cutting diameter | A1 | 10 mm / 0.394 inch |
Peripheral effective cutting edge count | F21 | 4 |
Corner chamfer width | G2 | 0,2 mm / 0.008 inch |
Corner chamfer angle | G3 | 45 ° |
Cutting edge length, max. | B2 | 22 mm / 0.866 inch |
Overalllength | B5 | 73 mm / 2.874 inch |
Head length | B6 | 22 mm / 0.866 inch |
Neck diameter | A5 | 9,5 mm / 3/8 inch |
Neck length | B9 | 30,5 mm / 1.201 inch |
Connection diameter, machine side | C3 | 10 mm / 0.394 inch |
Tolerance class connection diameter ISO tolerance | C31 | h6 |
Shanklength | C4 | 40 mm / 1.575 inch |
Helix angle | F4 | 32 ° |
Mass (weight) | D7 | 0,071 kg |
Standard number of properties layout | NSM | DIN4000-82 |
Corner design | F72 | 2 - |
Usable length | B4 | 22 mm / 0.866 inch |
Protruding length | B3 | 40 mm / 1.575 inch |
Functional length | B71 | 73 mm / 2.874 inch |
item style code | BLD | 2 |
Connection code type machine side | C11 | ZYL |
Connection code form type machine side | C12 | 01 |
Connection code style machine side | C15 | 5 |
Connection size code machine side | C2 | 100 |
Connection code style tolerance class machine side | C16 | h$06 |
mill tool type ISO | D11 | H |
Hand | F1 | R |
flute helix hand | F3 | R |
face effective cutting edge count | F22 | 4 - |
cutting edge centre count | F27 | 1 - |
grade manufacturer's designation | H3 | D |
Coating | H5 | A |
Cutting tool type | H4 | H |
grade standard designation, main application | H11 | VHM |
Company identification | J3 | HAI |
interface code to machine side | J6 | ZYL01000105 |
machining process | J8 | FEC,FNB,FSE, FZI,FNU |
Shank diameter, upper limit | C32 | 10 mm / 0.394 inch |
Shank diameter, lower limit | C33 | 9,991 mm / 0.393 inch |
Transition radius 2 | E74 | 8,125 |
Description | Norm: ISO 13399 | Value: metric/inch |
---|---|---|
Weight | WT | 0,071 kg |
Characteristics
Corner chamfer 45°
Teeth 4
Helix angle 31/33°
Applications
- For almost all materials
- For roughing and finishing
- For ramping, drilling and slotting
AREAS OF APPLICATION - MATERIAL
MAIN AREA OF APPLICATION
Steel
All types of steel and cast steel, with the exception of steel with an austenitic structure
Stainless steel
Stainless austenitic steel and austenitic-ferritic steel and cast steel
FURTHER AREAS OF APPLICATION
Cast iron
Grey cast iron, cast iron with spheroidal graphite, malleable cast iron, cast iron with vermicular graphite
High temperature alloys and titanium alloys
Heat resisting special alloys based on iron, nickel and cobalt, titanium and titanium alloys
NF metals
Aluminium and other non-ferrous metals, non ferrous materials
Hard materials
Hardened steel, hardened cast iron materials, chilled cast iron
Operations
Feed direction (Side milling, Ramping, Drilling)
Ramping
Slotting
Side milling
Drilling
Cooling
Emulsion
Cold air
Dry machining
Minimal lubrication